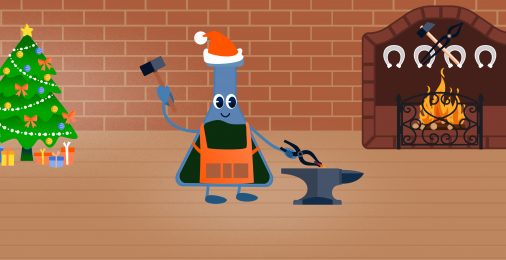
Металлургия зародилась за тысячи лет до нашей эры, древние египтяне умели делать украшения из сплава золота и серебра, а оружие — из метеоритной стали. На протяжении веков технологии совершенствовались: металлурги искали оптимальную конструкцию печи и придумывали, чем лучше ее разогревать. В качестве топлива использовали древесину, уголь, мазут, газ, но, как оказалось, лучше всего плавить сталь электрическим током. В современных электродуговых печах используют полутораметровые электроды из игольчатого кокса — это богатый углеродом твердый материал, получаемый при переработке нефти. «Энергия+» разобралась, как его производят.
Иголки жидкого кристалла
Свое название игольчатый кокс получил благодаря необычной структуре, напоминающей спрессованные иголки. Особое строение наделяет материал необычными свойствами: он хорошо проводит электричество и тепло только в заданном направлении — вдоль своих иголок. Это делает игольчатый кокс востребованным в металлургии: из него производят графитированные электроды для высоконагруженных сталеплавильных печей. Они выдерживают температуру свыше 4000 градусов, отличаются высокой электропроводностью и механической прочностью.
Игольчатый кокс нужен не только для графитированных электродов. Это незаменимый материал для производства литий-ионных аккумуляторов.
Сырьем для игольчатого кокса служит смесь жидких углеводородов, внешне напоминающая растительное масло, — тяжелый газойль. Он остается после переработки тяжелых фракций нефти методом каталитического крекинга, в процессе которого большие и тяжелые молекулы под воздействием температуры и катализаторов распадаются.
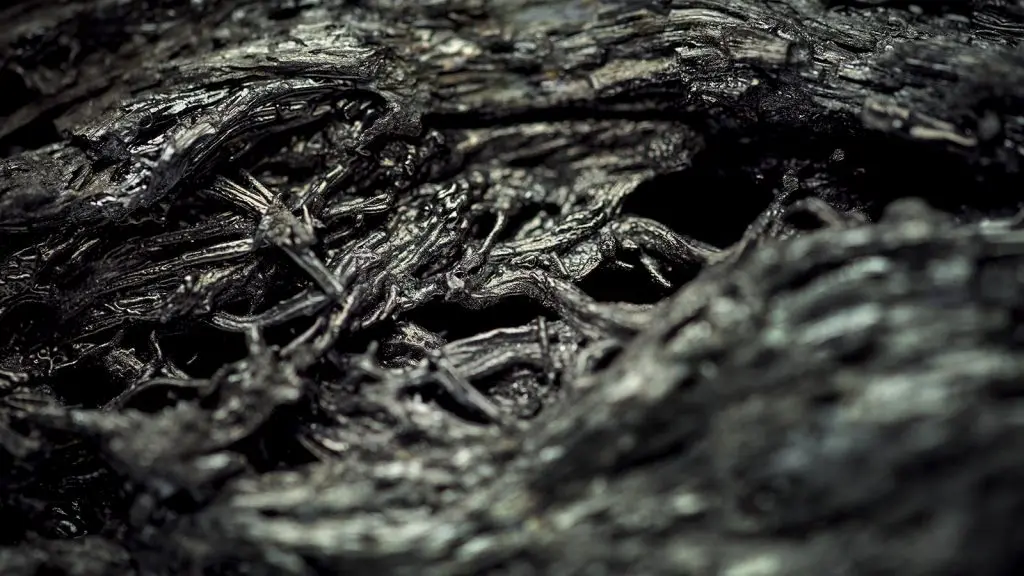
В тяжелом газойле много ароматических углеводородов. При коксовании (нагреве без доступа воздуха), прежде чем превратиться в твердый материал, они образуют жидкокристаллическую структуру. Именно в таком состоянии у кокса вырастают иголки.
Очистить, но только от серы
В составе тяжелого газойля есть сера — нежеланный компонент, который может снизить качество металла при выплавке, уменьшить прочность и электропроводность электрода.
Для удаления серы разработали технологию гидроочистки газойля. В стандартном варианте она удаляет серу и ароматические соединения, но при производстве игольчатого кокса необходимо удалить только серу. В результате избирательной гидроочистки содержание серы в газойле снижается в несколько раз, а ценные углеводородные структуры сохраняются.
Без кислорода при 450 градусах
Для получения игольчатого кокса используют установки замедленного коксования. Объем каждой камеры — около 450 кубических метров, как у стандартного плавательного бассейна. Внутри давление до 4 атмосфер и нет кислорода. Например, на Омском нефтеперерабатывающем заводе четыре камеры, из них две поочередно заняты в производстве. Нагретые газы остывающих камер подогревают две работающие, повышая энергоэффективность технологии.
В процессе коксования сырье при температуре 450–500 градусов поступает в камеру. Из него выделяются углеводородные газы, а остатки тяжелых нефтепродуктов, которые не успели превратиться в кокс, возвращаются на повторный цикл коксования: этот прием увеличивает выход и качество кокса.
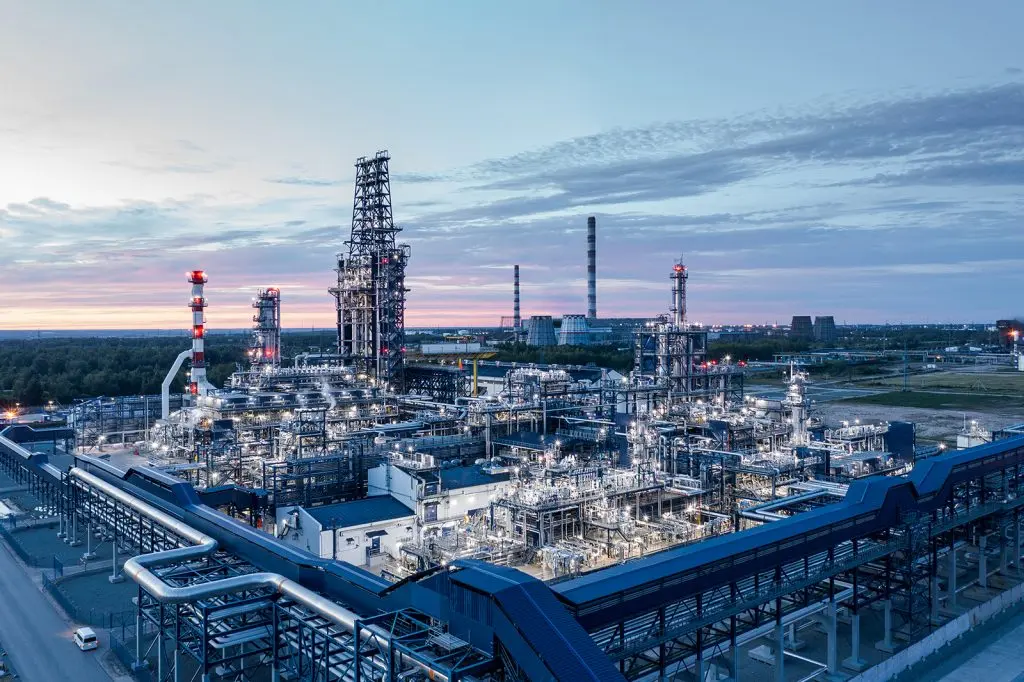
Готовый кокс охлаждают, извлекают из камер, прокаливают и отправляют на предприятие по производству графитированных электродов. Там его измельчают до частиц нужного размера и пропитывают пеком — густой и тяжелой углеводородной жидкостью, образующейся при переработке угля или нефти. Такая пропитка позволяет при обжиге «запечатать» пустоты между частичками кокса, чтобы сделать его прочнее и однороднее. Благодаря пропитке кокс можно прессовать в изделия нужной формы.
Пропитка делает кокс более устойчивым к высоким температурам, улучшает его электропроводность и прочность. Напоследок материал для электродов графитируют при температуре более 2300 градусов.
9 шагов для получения графитированных электродов
- Гидроочистка газойля от серы.
- Транспортировка в камеры установок замедленного коксования.
- Нагрев до 450 градусов.
- Запуск и поддержание процесса коксования (24–32 часа).
- Охлаждение камеры.
- Выгрузка застывшего кокса, его отделение от стенок при помощи бура с гидравлическим приводом.
- Сушка, измельчение и пропитка.
- Графитирование при температуре более 2300 градусов.
- Прессование до нужного размера.
В результате получаются графитированные электроды, способные работать внутри сверхмощных сталеплавильных печей. За счет низкого удельного сопротивления (8–13 микроом на метр) они могут отдавать электричество с меньшими потерями, а благодаря пониженному содержанию золы — оставаться прочными и оставлять чистой сталь.