В Нижнем Новгороде придумали, как из углекислого газа сделать электролиты для аккумуляторов и обойтись без токсичных веществ и дорогих катализаторов
Новую технологию переработки углекислого газа (СО2) в полезные продукты разработали ученые из Нижегородского государственного университета имени Н. И. Лобачевского (ННГУ). Метод позволяет упростить и удешевить процесс получения циклических карбонатов. Это природные растворители, жидкие или легкоплавкие твердые вещества, используемые как сырье для производства материалов, например поликарбоната, которым садоводы покрывают теплицы.
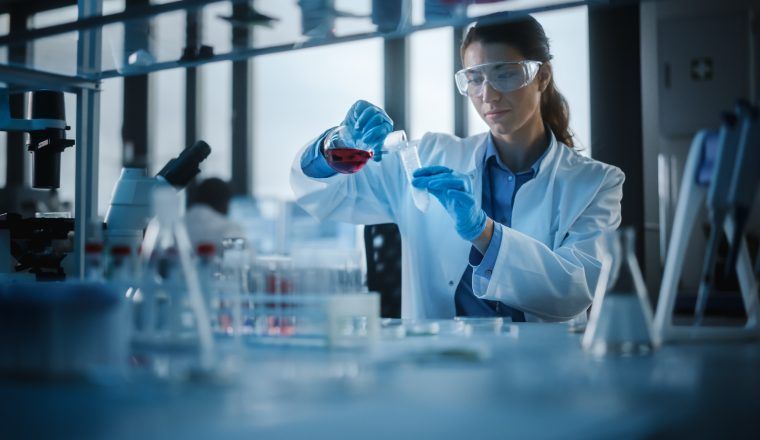
Применяют циклические карбонаты и в качестве электролитов — растворов водных солей, щелочей и кислот с большим содержанием ионов, обеспечивающих прохождение электрического тока. Электролиты — основной компонент литий-ионных аккумуляторов.
Сегодня циклические карбонаты получают с использованием ядовитого газа фосгена или катализаторов на основе металлоорганических соединений. В первом случае применяется токсичное сырье, во втором — вещества, которые эффективны только при высоком давлении до 25 атмосфер и температуре около 150 градусов Цельсия. Кроме того, такие катализаторы нужно утилизировать после однократного использования.
Нижегородские ученые предложили заменить «капризные» катализаторы на менее прихотливые, созданные на основе полимерных ионных жидкостей. Такие катализаторы работают при температуре до 100 градусов Цельсия и атмосферном давлении и могут использоваться повторно без потери свойств.
«В нашей технологии в установку помещается жидкое сырье — оксид алкена и полимерный катализатор в порошкообразном виде. После нагрева до 70 градусов Цельсия через установку слабым потоком продувается углекислый газ. В результате в колбе, в которой было изначальное сырье, образуются жидкие циклические карбонаты», — рассказала руководитель авторского коллектива аспирантка ННГУ Анна Головачева.
Ученые полагают, что, по сравнению с существующими, новая технология даст 15–20% экономии за счет меньшего потребления электроэнергии для нагрева катализатора и отсутствия дорогостоящей установки, работающей при высоком давлении. На данный момент в институте проходит этап лабораторных исследований, в дальнейшем предполагается масштабирование технологии до промышленного производства.